Why plastic extrusion is perfect for mass production
Why plastic extrusion is perfect for mass production
Blog Article
Discovering the Various Methods and Technologies Behind Plastic Extrusion
The realm of plastic extrusion is a mix of technology, accuracy, and technology, pivotal to numerous industries worldwide. Advanced equipment, electronic controls, and a range of products converge in this complex procedure, generating top notch, sturdy items.
Comprehending the Basics of Plastic Extrusion
The process of plastic extrusion, frequently hailed as a cornerstone in the realm of manufacturing, creates the bedrock of this conversation. In essence, plastic extrusion is a high-volume production process in which raw plastic material is thawed and developed right into a continual profile. It's an approach commonly utilized for producing things with a continuous cross-sectional profile, such as pipelines, home window frames, and climate stripping. The procedure begins with feeding plastic products, frequently in the kind of pellets, into a heated barrel. There, it is blended and heated till it comes to be molten. The liquified plastic is then required via a die, shaping it right into the wanted form as it solidifies and cools.
The Function of Different Materials in Plastic Extrusion
While plastic extrusion is a frequently used method in manufacturing, the materials made use of in this procedure substantially influence its last output. Various types of plastics, such as polyethylene, abdominal, and pvc, each offer unique buildings to the end product. Manufacturers have to thoroughly think about the homes of the material to optimize the extrusion procedure.
Methods Utilized in the Plastic Extrusion Process
The plastic extrusion procedure involves numerous methods that are essential to its procedure and performance (plastic extrusion). The conversation will begin with a simplified description of the essentials of plastic extrusion. This will be adhered to by a breakdown of the process thoroughly and an exploration of approaches to enhance the effectiveness of the extrusion strategy
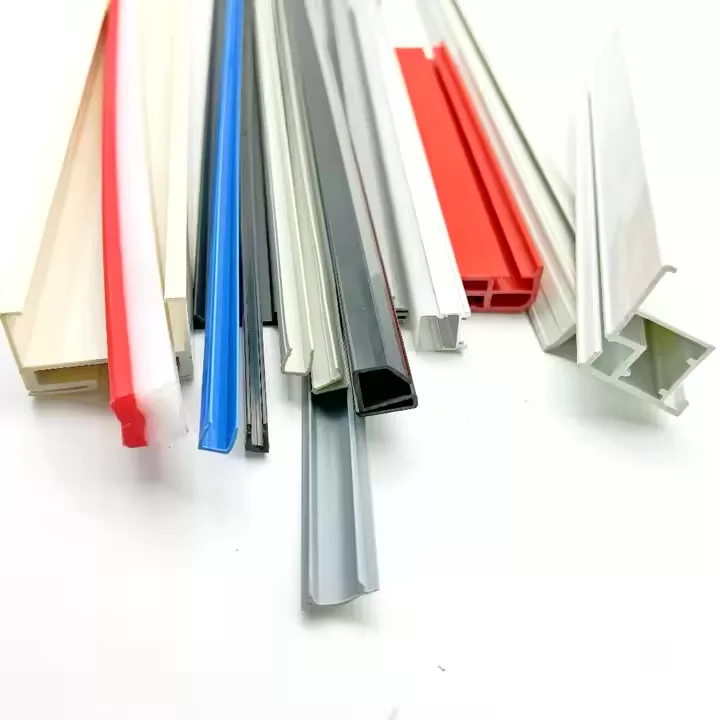
Comprehending Plastic Extrusion Basics
In the realm of manufacturing, plastic extrusion stands as a fundamental process, necessary in the manufacturing of a multitude of day-to-day products. At its core, plastic extrusion includes changing raw plastic product right into a continual profiled form. Basic understanding of these basics allows for further expedition of the much more detailed aspects of plastic extrusion.
Thorough Extrusion Refine Breakdown

Improving Extrusion Technique Effectiveness
Effectiveness gains in the plastic extrusion procedure can substantially affect both the high quality of the last item and the overall performance of the operation. Constant optimization of the extrusion method is important to keeping an one-upmanship. Techniques that boost efficiency usually entail specific control of temperature and stress throughout the process. Modern technologies, such as electronic systems and sensors, have been crucial in achieving this control. The use of top notch raw materials can lower waste and enhance result top quality. Regular maintenance of extrusion tools can likewise lessen downtimes, therefore boosting performance. Lastly, taking on lean production concepts can help eliminate unneeded actions in the process, promoting effectiveness gains.
Just How Technology Is Transforming the Face of Plastic Extrusion
The development of brand-new modern technology has actually significantly transformed the landscape of plastic extrusion. It has brought about the advancement of innovative extrusion machinery, which has enhanced the effectiveness and top quality of the plastic extrusion process. Furthermore, advancements in the extrusion procedure have actually web likewise been driven by technical improvements, supplying boosted abilities and flexibility.
Advanced Extrusion Equipment
Changing the world of plastic extrusion, progressed equipment imbued with advanced modern technology is ushering in a new period of effectiveness and accuracy. These devices, furnished with cutting-edge features like automatic temperature level control systems, guarantee optimum conditions for plastic processing, thus minimizing waste and boosting item top quality. High-speed extruders, as an example, magnify output prices, while twin-screw extruders use remarkable mixing capacities, vital for creating complicated plastic blends. Furthermore, electronic control systems supply unprecedented precision in procedures, reducing human mistake. Furthermore, these makers are designed for longevity, lowering downtime and upkeep prices. While these developments are currently remarkable, the continual evolution of technology guarantees also higher jumps forward in the area of plastic extrusion equipment.
Innovations in Extrusion Procedures
Taking advantage of the power of contemporary technology, plastic extrusion procedures are undergoing a transformative transformation. Developments such as electronic numerical control (CNC) systems currently permit more precision and directory uniformity in the manufacturing of extruded plastic. Automation better enhances performance, decreasing human error and labor expenses. The assimilation of man-made knowledge (AI) and equipment learning (ML) algorithms is revolutionizing quality assurance, forecasting discrepancies, and enhancing the total performance of extrusion processes. With the introduction of 3D printing, the plastic extrusion landscape is likewise broadening right into brand-new worlds of possibility. These technological advancements are not just improving the quality of extruded plastic items but additionally driving the industry in the direction of a more lasting, efficient, and innovative future.
Real-World Applications of Plastic Extrusion
Plastic extrusion, a efficient and versatile process, discovers usage in many real-world applications. The auto sector additionally uses this technology to produce components like plastic and trim sheet. The stamina and flexibility of plastic extrusion, combined with its cost-effectiveness, make it a crucial procedure throughout numerous markets, highlighting its extensive functional applications.
The Future of Plastic Extrusion: Forecasts and Patterns
As we look to the perspective, it ends up being clear that plastic extrusion is positioned for significant developments and transformation. Green options to conventional plastic, such as bioplastics, are likewise anticipated to obtain traction. These trends indicate a dynamic, evolving future for plastic extrusion, driven by technical advancement and a commitment to sustainability.

Conclusion
In final thought, plastic extrusion is a complicated process that uses sophisticated innovation and varied materials to create diverse products. As plastic production continues to evolve, it remains an important part of numerous industries worldwide.
In essence, plastic extrusion is a high-volume manufacturing procedure in which raw plastic product is thawed and developed into a constant profile.While plastic extrusion is a frequently made use of technique in manufacturing, the materials made use of in this procedure greatly influence its final outcome. At its core, plastic extrusion involves changing raw plastic product right into a constant see this profiled form. It has led to the development of advanced extrusion equipment, which has actually improved the performance and top quality of the plastic extrusion process.In conclusion, plastic extrusion is a complex procedure that makes use of innovative technology and differed products to create diverse products.
Report this page